SafeZone 3 CIP Safety Area Scanner
GERRIE ROCKWELL AUTOMATION GROUP - Safety -December 2021
By Christian Bidner
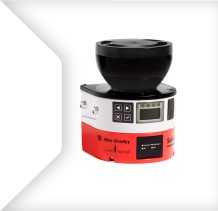
In writing this Blog about the new SafeZone 3 CIP Safety Area Scanner, I wanted to concentrate on four key points:
- CIP Safety connection over EIP
- New upgrade electronics to help mitigate dust/dirt/contamination issues that affect false tripping
- Multi-Field of view and simultaneous field set monitoring
- Studio 5000 imbedded set up software and Add-On-Profile (AOP)
First, let us get the most obvious fact out of the way (since the information is in the title of the Scanner!):
I’m referring to the CIP Safety connection capability of the new ScafeZone 3 Area Scanner. This means connection of the scanner to a Rockwell Safety PLC system is as simple as setting up a node on Ethernet IP and providing an address. All safety related communications and set up is now conducted through this EIP Port. On a side note, there are actually two ports. So, the scanner can be used in a Device Lever Ring (DLR) topography. This CIP Safety connection means that hard wiring of the safety outputs (OSSD), Aux Outputs, and field change inputs are no longer required. This is now all done through the CIP Safety connection, to the Rockwell Safety PLC. This significantly saves on time and material cost when communicating to, or setting up, the scanner.
Rockwell has upgraded the SafeZone 3 with new electronics that not only increase the range of the scanner to 5.5 meters (Safety Distance) but also improves its immunity to dust/dirt and other environmental conditions. A longer range means that this scanner can actively cover a larger area, and therefore provide more protection to workers, without having to use more scanners. High Definition Distance Measuring Scanning technology allows the scanner to become more resilient to environmental conditions that would, in the past, cause the scanner to “false trip”. This new scanning technology uses multiple pulses for each measurement and new data filtering/algorithms to help ignore dust, dirt or other contaminants that can affect the performance of the scanner. This means the scanner will operate more reliably and therefore provide less downtime due to cleaning or false tripping problems. The less a machine stops for cleaning of a scanner lens, or chasing false trips, the more productive and profitable a machine is…
Another enhancement has been made to the number of Fields that can be programmed, and the number of protective Field Sets that can be simultaneously monitored. The SafeZone 3 now can be configured with up to 8 Fields, and each Field can simultaneously monitor 4 separate protective Field Sets. (See example of the 4 separate protective Field Sets, inside one Field)
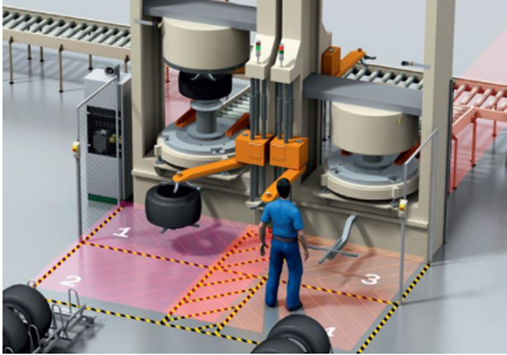
In this example, a single SafeZone 3 is monitoring 4 separate Field Sets (See above 1 to 4), while receiving input from the Robot arm’s position. By knowing what Field Set the robot is operating in, the control system, with the use of the scanner, can ensure that the Operator and the Robot are never in the same Field Set together or else a stop signal is sent. If the operator is not in the same Field Set as the Robot, the system is allowed to keep running. This way would allow the operator to Load or unload the product, while the robot continues to feed the rest of the machine. Based on this capability, machine owners would see a 50% increase in productivity, and therefor a higher profitability, compared to older (previous generation) Field Set scanners.
Lastly, Rockwell makes the integration, set up and programming easy. The Add On Profile (AOP) for the SafeZone 3 are available from Rockwell’s AOP Download center (Rockwell Automation Download Home) and are used within Studio 5000 Logix Designer. The AOP allows the user to enable communications with the scanner and immediately have access to preconfigured Tags. This saves a lot of time converting data assemblies to Tags list (and not making mistakes). The Tags can then be use on in the programming environment of Studio 5000 Logix Designer. EDS Files are available from the PCDC web site: Search PCDC Results (rockwellautomation.com)
Rockwell also provided the software tool to setup and program the SafeZone 3 scanner and its multiple Fields and Field Sets, inside Studio 5000 Logix Designer (Field Set Configuration). No need to download another piece of software, it’s already included. This software allows you to perform your traditional setup, such as configuring your Fields and Field Set, Range and Resolution, Scan times and Scan rates. You can also set up triggering events for the Field changes. Diagnostic information is also available if you need help to Troubleshoot the scanner or the existing program.
For further information such as detailed technical spec’s, installation instructions, configuration video, please visit the Rockwell web page: SafeZone Safety Laser Scanners | Allen-Bradley United States (rockwellautomation.com)
If you have any questions or would like to schedule an application review or demonstration, please feel free to contact myself at Gerrie Electric.
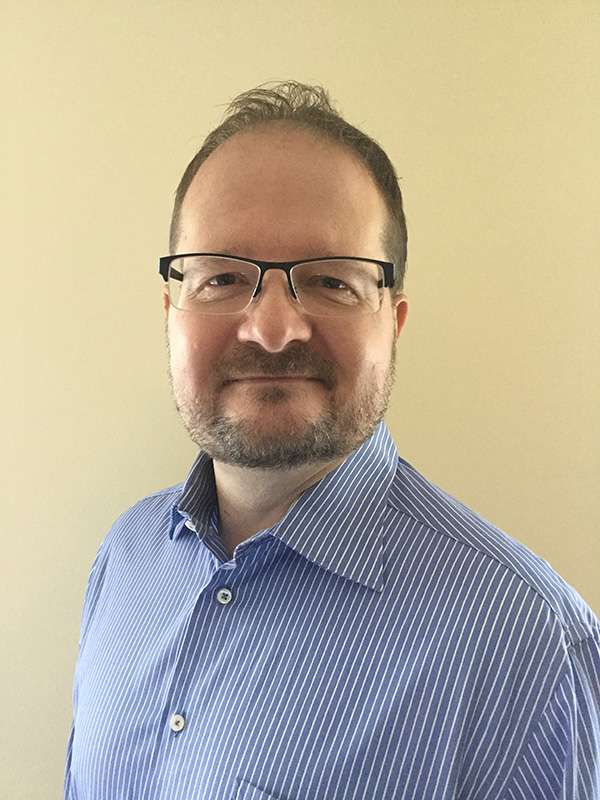
About The Author
Safety Product Manager, FS Eng.TÜV Rheinland, Machinery 12038/16, for Gerrie Electric in Burlington ON, Canada
C# 416-436-9706, DID 905-631-2781, [email protected],
Have Safety questions, click here to book a time with me for a one-on-one.