Pairing Rockwell Automation programmable control with the Plex Smart Manufacturing Platform leads to reduced downtime
Jason Morrow is a controls technician with Summer Garden Food Manufacturing. The company manufactures and packages products for the retail and food service markets including various barbecue and pasta sauces.
With an operation that runs two 12-hour shifts a day, 5 days a week and produces up to 100,000 cases of sauces weekly, overall equipment effectiveness (OEE) is a priority. But until Summer Garden Food installed the Plex Smart Manufacturing Platform™ in late 2022, they lacked the data visibility needed to ensure equipment was performing as efficiently as possible.
“We were missing downtime. We knew we had it, but we couldn't find it. Our kettle yields weren't equaling our run times. We wanted to start tracking downtime at a more detailed level than the piece of paper the operator writes,” Jason explains. “Plex is easily scalable. We could start with one machine and then build off that once we knew what we're doing. The scalability was one of the biggest reasons we went with Plex.”
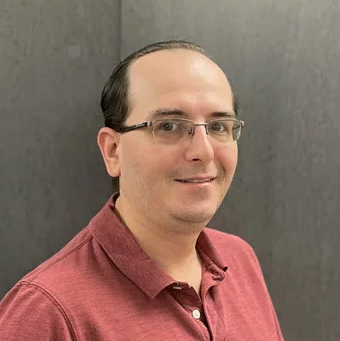
Jason Morrow
Controls Technician
Summer Garden Food Manufacturing
Summer Garden Food Manufacturing Increases Uptime
Watch the interview with Jason Morrow, Controls Technician, to hear how Plex Smart Manufacturing Platform has helped Summer Garden Food Manufacturing detect and address micro-downtime events.
Downtime Minutes Add Up
The first task for Summer Garden Food Manufacturing was tracking downtime on a key piece of equipment: the filler machine. The machine’s processes are controlled by Rockwell Automation 5300 series ControlLogix programmable controllers, which meant they were already collecting a lot of data. Using the Plex Smart Manufacturing Platform, the food manufacturer was able to easily program and extract data reports that pulled data from the Rockwell Automation controllers and several other sources.
“We found we had four hours of downtime per shift. Operators were repeatedly opening the door which stops the machine, making adjustments, and then closing the door. A minute here, two minutes there, five minutes here add up substantially throughout a shift,” Jason says. “But the operators weren’t writing it down. They didn’t think it was anything big. Yet, three to four hours of downtime a shift is a ton of downtime.”
With that valuable insight, the company is now focused on improving operator training and control to help improve machine performance. One tactic Summer Garden Food Manufacturing is undertaking is development of a visualization screen that provides operators insight into their personal daily OEE to facilitate individual awareness and growth.
Increasing Production with Further Machine Visibility
Next on its digital transformation journey, Summer Garden Food Manufacturing plans to expand the number of machines on its Plex platform.
“We started small. Now we’re going to branch out to the machines further down the line that may be causing the filler idle time. I'm sure there's micro downtime we're missing on the rest of the machines,” Jason explains. “There should be a ton of information. It's just digging into all that and eventually it should increase production.”
From there, Summer Garden Food Manufacturing will analyze manufacturing data by product, such as comparing the run times of different sauces.
“How do we improve the operation of the red sauce or the barbecue sauce so we can get the same speeds out of each product?” Jason offers as an example. “We have so many options when it comes to Plex. And it’s so simple whether it’s an add-on module or extra programming. You couldn’t ask for anything easier than that.”
Contact Gerrie Rockwell Automation Team