Driving Performance for Food & Beverage Manufacturers
We understand the challenges you face in daily food and beverage manufacturing operations, such as supply chain disruptions, food safety, recalls, and tighter compliance requirements. To help you overcome the increasing industry demands while remaining competitive, we developed a comprehensive digital solutions portfolio that will boost your productivity and resource utilization efficiency while empowering workers to make smart data-driven decisions throughout the plant floor.
Our digital solutions help small, midsize, and extensive food and beverage manufacturing facilities minimize downtime, reduce costs, and maximize asset and resource utilization by providing visibility into production workflows, enabling proactive maintenance strategies, and eliminating inefficient paper-based tasks.
Applications for Food and Beverage Industry
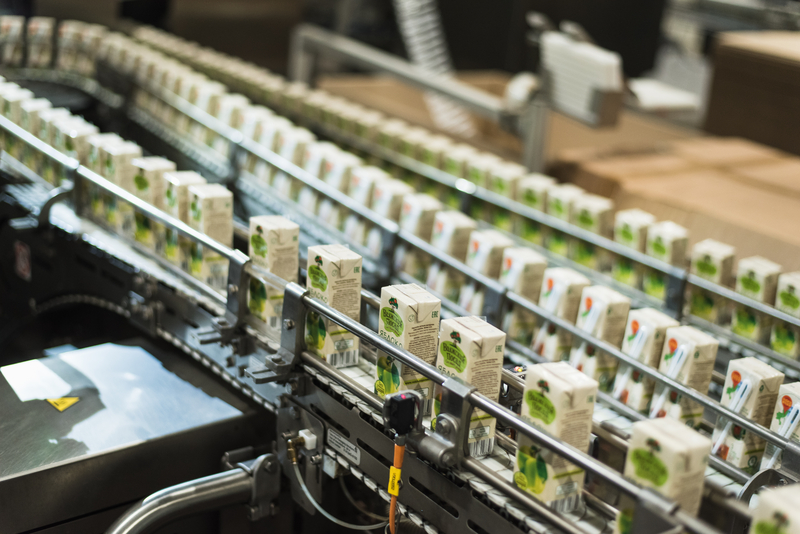
Maximize Operational Efficiency
With a flexible and modular digital solution, you can control your manufacturing operations anywhere on the plant floor. Additionally, integrate the different work centers to streamline plant operations, reduce waste, maximize resource utilization, and enable continuous improvement actions.
Another key advantage is the adoption of environment-friendly practices that meet government requirements and conscious consumer demands.
Quality Control & Compliance Management
Defects and non-compliant practices can lead to costly recalls and damage to brand reputation. An integrated quality management system improves internal quality processes and ensures adherence to quality regulatory standards. It streamlines quality control activities and facilitates continuous improvement throughout the shop floor.
Take data-driven insights that will enable continuous improvement of quality control processes. Track & Trace capabilities allow for real-time detection of production line defects so defective items can be segregated safely, preventing client complaints and damage to brand reputation.

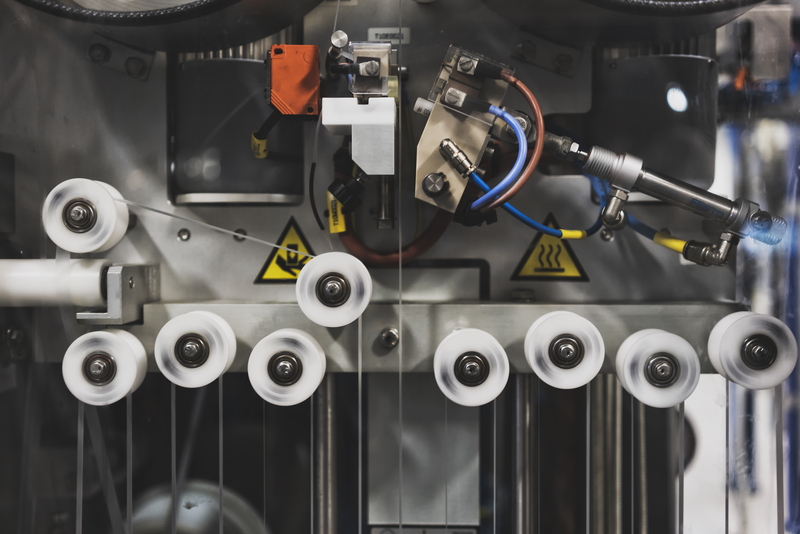
Minimize Unplanned Equipment Downtime
Get alerts for out-of-range parameters and early signs of equipment failures to replace parts before causing equipment downtime and keep constant track of asset health to maximize asset uptime.
Additionally, it enables a more efficient labor resource allocation, a complete record of work orders, parts, supplies management, AI-driven anomaly detection capabilities, and many more features.
Your maintenance team can prioritize work orders based on equipment data and manage spare parts efficiently.
Â
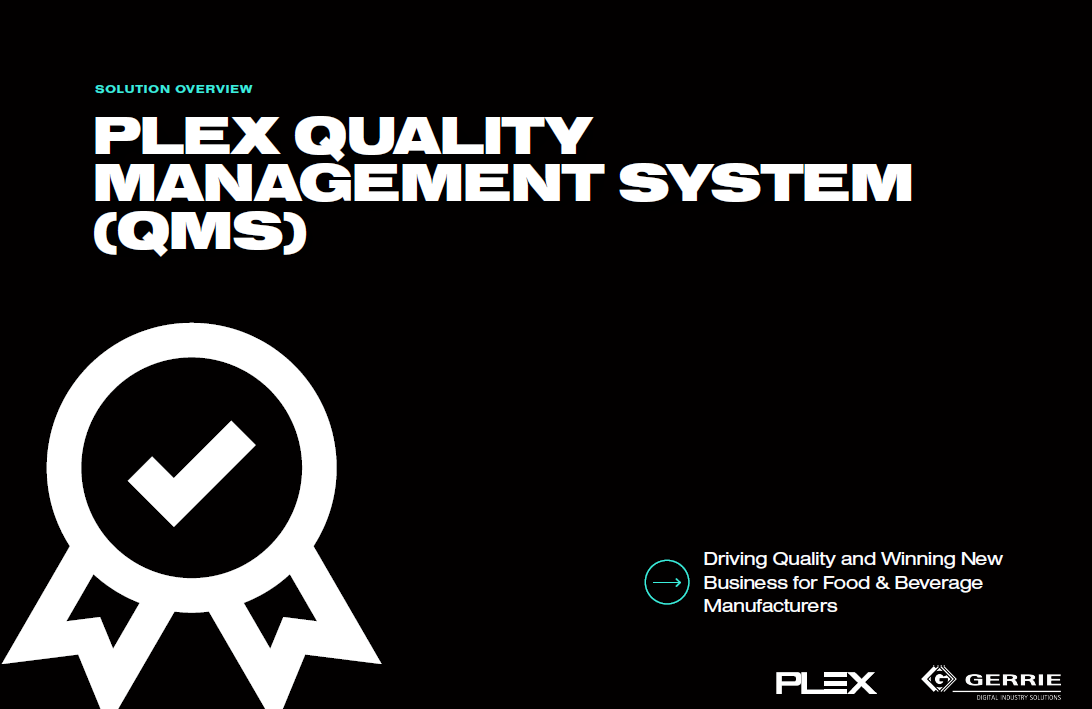
Â
Elevate Food & Beverage Quality Control: Automate, Comply, and Succeed
The Plex Quality Management System (QMS) for the food and beverage industry provides a comprehensive digital solution to ensure product quality, regulatory compliance, and operational efficiency. By automating quality processes and real-time data capture, Plex QMS helps food and beverage manufacturers eliminate manual errors, improve traceability, and maintain high standards amidst increasing regulatory pressures.
The system ensures compliance with industry standards like HACCP and FSMA while preventing costly recalls and enhancing customer satisfaction. For quality control leaders, Plex QMS offers the tools to proactively manage and monitor production, ensuring consistent delivery of top-quality products.
Download the brochure to learn more!
Download Here
Frequently Asked Questions
Can I share information with my team and other departments?
Our smart manufacturing solutions integrate all your manufacturing systems onto a high-availability cloud-based platform, which allows the collection and analysis of real-time production data.
The platform provides all departments with a unified view of multiple aspects of your facility. This supports production execution and monitoring, predictive maintenance, quality management, and inventory control to drive efficiency across the enterprise.
How much does it cost?
Our solutions are primarily cloud-based, and the cost can vary depending on your facility's size and specific requirements; in all cases where we deployed one of our digital solutions, the project resulted in significant ROI.
Contact us today to receive a tailored proposal for your facility outlining the pricing structure and features you can take advantage of.
How long is my data retained?
Forever. Your team can look back on any given period of time; the sooner your facility starts to collect data, the easier will be to make important data-driven decisions.
My facility operates 24/7. Is the solution available at all times?
Yes! Our digital solution is always up and running; this way, all departments can rely on fast and secure consolidated data during all working shifts.
Is the data collected from my facility safe online?
All communication to and from our data centers is encrypted, and secured using two-factor authentication technology. This way, only authorized users, with authorized devices can access the platform.
Can this solution be implemented on a single production line?
Yes. Modularity is one of the key advantages of our solution portfolio. You can deploy a digital solution for one or two work centers initially, and progressively expand it to other areas.
We Are Your Local Trusted Partner
Â
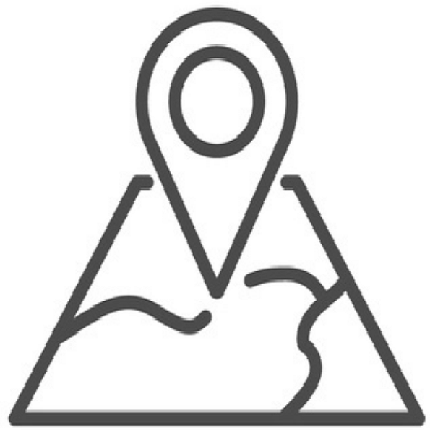
Â

Â
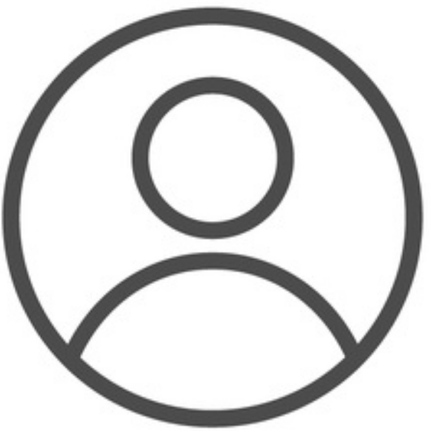
24 Ontario Locations
You can count on us at any time. One of our digital solutions experts is located close to you.
At Your Side Since 1957
Well-known and respected in the industry, with a strong reputation built on service.
400+ Team Members
Platinum Standard Winner of Canada's Best Managed Companies.
Â
Where Do I Go Next?
Schedule a complimentary technical consultation with our digital industry solutions experts for a tailored solution that fits your needs.
Â
Contact Us Now To Learn More!
Â
Head Office - Burlington, ON - Canada
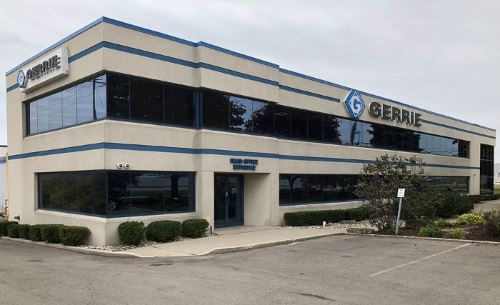
Â
Email: [email protected]
Phone:Â (905) 681-3668
Â
GERRIE DIGITAL INDUSTRY SOLUTIONS
Â
Passionately Helping Customers Be More Successful by Delivering Exceptional Experiences.
Copyright © Gerrie Electric Wholesale Limited. All Rights Reserved
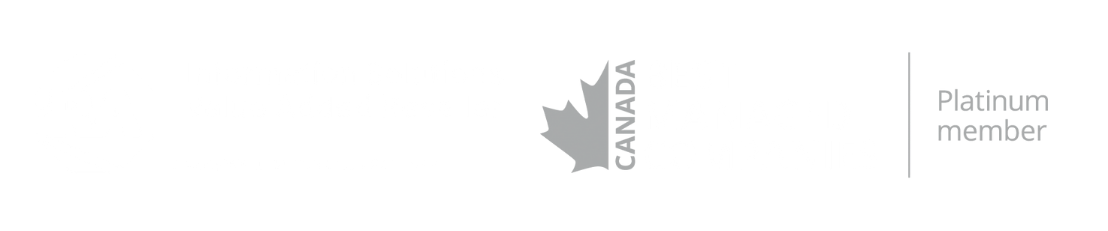