Applications For Industrial Quality ControlÂ
Â
Compliance Management Tools
Take advantage of a centralized repository for seamless control of documents that are required by certification entities, i.e. ISO 9001, FMEA, IATF 16949, OHSA, Control Plans, etc.
Your team can easily control document versions and update internally distributed documents instantly.
Detailed Scrap Report by Work Centers
Scrap numbers are imported directly from machines or added from work station via tablet in real-time.
With a single and reliable data source, there is no more scrap data discrepancies as it is automatically gathered from the work centers.
Digital Data Entry
Remove inefficient paperwork that later would need to be manually added into spreadsheets.
By removing Non-Value Activities (NVAs), your operations teams can dedicated to being more productive.
Continuous Improvement Enablement
Take data-driven decisions when prioritizing continuous improvement projects in the operations most critical stages.
This enables high-targeted projects, resulting in the highest possible ROI.
Continued Operator Onboarding Training
Identify which stage of the production flow is negatively impacting your operations throughput.
This capability empowers your facility to plan new production layouts, efficiently allocate machinery investments and drive target projects to address production bottlenecks.
Track & Trace Production Batches
With real-time visibility of production workflow, non-conformity batches can be easily identified and segregated.
This allows a prompt and efficient reaction in case of recalls or client complaints.
Quality Control KPIs Dashboards
With a user-friendly interface, you can use pre-made Quality Control dashboards or create custom ones to reflect the specific aspects of your operations.
Additionally, share reports with other team members and better collaborate with different departments.
Paperless Quality
Eliminate wasted time looking for paper-based SOPs. Your operation workers can easily consult digital SOPs to guarantee adherence to standard procedures, and new hires can also be easily trained with them.
If an SOP is modified, there is no need to worry that old versions might be still available on the production floor, as they replace old versions instantly.
Â

Â
Streamline Quality Control with Plex QMS
The Plex Quality Management System (QMS) brochure highlights how this cloud-based solution can help quality control leaders in manufacturing achieve superior product quality and compliance. It addresses key challenges like manual processes, lack of visibility, and difficulty in meeting regulatory standards.
Plex QMS automates quality management, providing real-time data, predictive insights, and a single source of truth for all quality documentation. This ensures repeatability, reduces the risk of recalls, and enhances customer satisfaction. With Plex QMS, manufacturers can streamline quality processes, maintain compliance, and drive continuous improvement in a competitive market.
Download Here
Â
Frequently Asked Questions
Can I share information with my team and other departments?
Our smart manufacturing solutions integrate all your manufacturing systems onto a high-availability cloud-based platform, which allows the collection and analysis of real-time production data.
The platform provides all departments with a unified view of multiple aspects of your facility. This supports production execution and monitoring, predictive maintenance, quality management, and inventory control to drive efficiency across the enterprise.
How much does it cost?
Our solutions are primarily cloud-based, and the cost can vary depending on your facility's size and specific requirements; in all cases where we deployed one of our digital solutions, the project resulted in significant ROI.
Contact us today to receive a tailored proposal for your facility outlining the pricing structure and features you can take advantage of.
How long is my data retained?
Forever. Your team can look back on any given period of time; the sooner your facility starts to collect data, the easier will be to make important data-driven decisions.
My facility operates 24/7. Is the solution available at all times?
Yes! Our digital solution is always up and running; this way, all departments can rely on fast and secure consolidated data during all working shifts.
Is the data collected from my facility safe online?
All communication to and from our data centers is encrypted, and secured using two-factor authentication technology. This way, only authorized users, with authorized devices can access the platform.
Can this solution be implemented on a single production line?
Yes. Modularity is one of the key advantages of our solution portfolio. You can deploy a digital solution for one or two work centers initially, and progressively expand it to other areas.
Where Do I Go Next?
Schedule a complimentary technical consultation with our digital industry solutions experts for a tailored solution that fits your needs.
Â
We Are Your Local Trusted Partner
Â
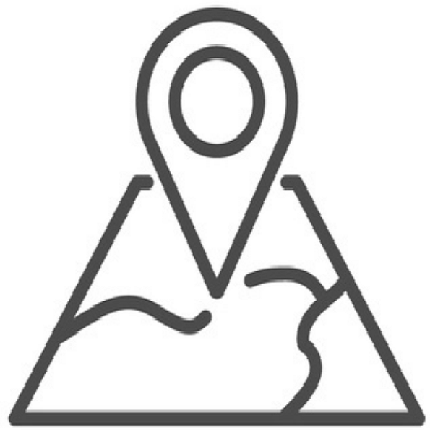
Â

Â
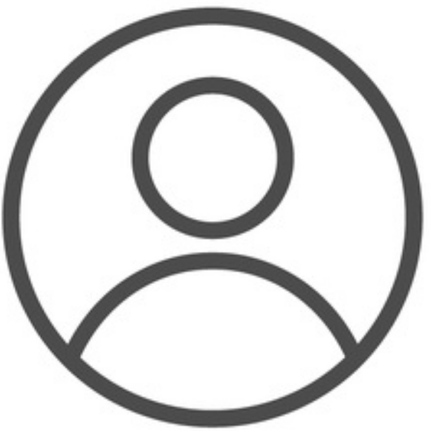
24 Ontario Locations
You can count on us at any time. One of our digital solutions experts is located close to you.
At Your Side Since 1957
Well-known and respected in the industry, with a strong reputation built on service.
400+ Team Members
Platinum Standard Winner of Canada's Best Managed Companies.
Â
Contact Us Now To Learn More!
Â
Head Office - Burlington, ON - Canada
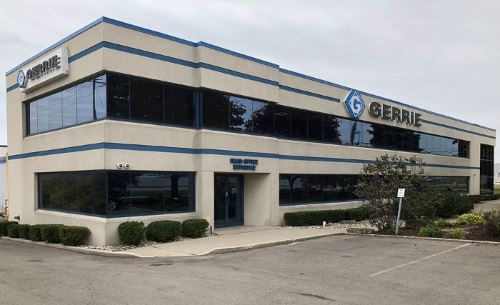
Â
Email: [email protected]
Phone:Â (905) 681-3668
Â
GERRIE DIGITAL INDUSTRY SOLUTIONS
Â
Passionately Helping Customers Be More Successful by Delivering Exceptional Experiences.
Copyright © Gerrie Electric Wholesale Limited. All Rights Reserved
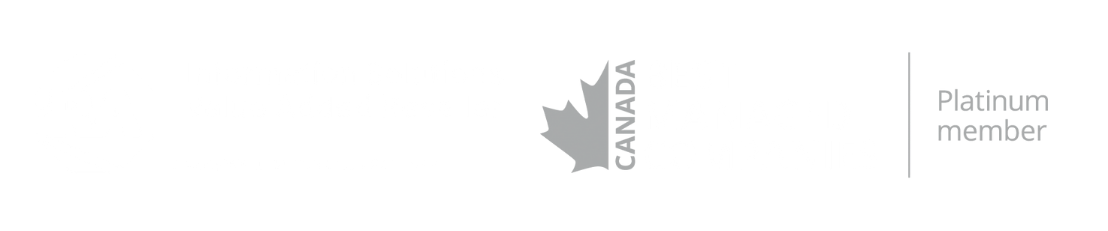