Digital Industry Solutions Blog
Top 10 Benefits of Real-Time Monitoring in Manufacturing
January 24, 2025
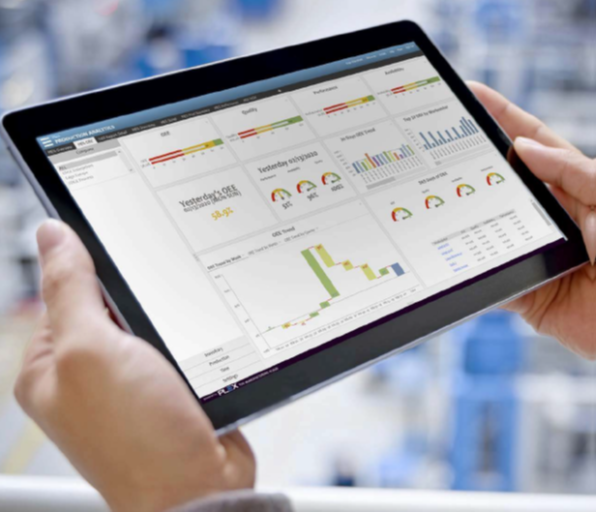
Modern manufacturing goals are no longer just about producing high-quality goods or large-scale outputs. Manufacturers are being pushed to do all that with the least resources and losses. With increasing demands for efficiency, quality, and sustainability, manufacturers from various sectors are adopting real-time monitoring technologies to remain competitive. Whether for tracking production lines in an automotive plant or ensuring food safety and traceability in a processing facility, real-time data provides the clarity and control needed to drive operational excellence. The ability to instantly detect inefficiencies (like bottlenecks), predict maintenance activities, and optimize resource utilization allows manufacturers to respond proactively, reducing waste and enhancing productivity.
By integrating real-time monitoring into daily operations, manufacturers can break down data silos between departments, fostering collaboration between production, maintenance, quality control and many other teams. It empowers decision-makers with the insights they need to make informed choices, ensuring that production schedules stay on track, minimizing equipment downtime, and ensuring consistent product quality, especially in the Food & Beverage and Automotive industries. In an environment where each productive second has a substantial price tag, day-to-day inefficiencies are no longer to be tolerated.
To exemplify how real-time monitoring has been a game changer in many industrial settings, let's explore the top 10 benefits of real-time monitoring in manufacturing with practical examples.
1. Improved Operational Efficiency
Efficiency is the backbone of any successful manufacturing operation. Real-time monitoring provides manufacturers with a comprehensive view of their production processes, identifying bottlenecks and inefficiencies as they arise.
For instance, a discrete parts manufacturer can track production cycles in real-time and detect process anomalies on the assembly lines. By analyzing data from sensors and IoT devices, production managers can adjust workflows, redistribute labour, and optimize throughput, all without disrupting operations. In the food industry, real-time monitoring helps track ingredient usage and minimize waste by ensuring production aligns with demand forecasts.
2. Reduced Downtime with Predictive Maintenance
Unexpected equipment failures are manufacturers' worst nightmares, often leading to costly delays and lost productivity. This is another front in which real-time monitoring systems excel by predicting potential downtime and early warning signs of equipment failure.
Consider a plant using real-time monitoring to track vibrations in critical machinery. By identifying abnormal patterns, maintenance teams can intervene before a breakdown occurs. Similarly, food processing facilities can monitor refrigeration units to ensure they remain within temperature thresholds, preventing spoilage and compliance issues.
3. Enhanced Quality Control
Maintaining high product quality is crucial, especially in industries with strict regulatory requirements, such as the food & beverage and pharmaceutical industries. Real-time monitoring enables manufacturers to track critical quality parameters continuously, ensuring products meet specifications.
For example, active monitoring systems track fill levels, packaging integrity, and product consistency in a beverage production facility in real time. Any deviation from quality standards triggers an immediate alert, allowing corrective actions before defective products reach customers. Automotive manufacturers can also monitor precision in welding processes to maintain stringent safety standards.
4. Increased Energy Efficiency
Energy consumption is one of the largest operational costs in manufacturing. Real-time energy monitoring allows manufacturers to identify inefficiencies and implement cost-saving measures without compromising productivity.
Discrete parts manufacturers use smart energy monitoring to track power consumption across different production lines. Insights from real-time data help identify peak usage periods, allowing facilities to adjust operations for maximum energy savings. In the food industry, monitoring helps optimize energy usage in refrigeration, baking, and processing lines.
5. Better Compliance and Regulatory Adherence
Manufacturing operations must comply with numerous industry regulations and standards. Real-time monitoring software solutions offer automated compliance tracking and documentation version control, making it easier to meet regulatory and certification requirements.
6. Optimized Supply Chain Management
A well-optimized supply chain is crucial to meeting production targets and fulfilling customer demands. Real-time monitoring enhances supply chain visibility, allowing manufacturers to respond proactively to imminent disruptions.
Discrete parts and process manufacturers rely on real-time data to track the availability of raw materials, ensuring production schedules remain on track. Food manufacturers use real-time monitoring to manage inventory levels and reduce the risk of spoilage or overstocking.
7. Enhanced Safety and Risk Management
Workplace safety is a top priority in manufacturing, and real-time monitoring plays a vital role in reducing risks and preventing workplace accidents. Sensors and monitoring systems provide instant feedback on environmental conditions, equipment performance, and safety compliance.
For example, a chemical manufacturing facility might use sensors to monitor hazardous gas levels on its shop floor, triggering alarms when thresholds exceed acceptable levels.
8. Strengthened Cybersecurity and IT/OT Integration
With more devices, sensors, and machinery connected to the network, the risk of cyber threats increases significantly. Real-time threat monitoring is crucial in strengthening cybersecurity by providing continuous visibility into IT and OT environments, allowing manufacturers to detect and respond to potential threats. By implementing real-time cybersecurity monitoring, manufacturers can proactively safeguard their assets, protect sensitive data, and ensure business continuity. The result is a more resilient and secure production environment where IT and OT teams can collaborate effectively to mitigate risks and maintain seamless operations.
9. Improved Collaboration Across Departments
Real-time monitoring fosters collaboration by providing a centralized platform on which different departments, such as operations, maintenance, and quality control, can access and act on unified, shared data.
For instance, maintenance teams in an automotive plant can work closely with production managers to plan repairs without disrupting workflows. In food manufacturing, quality control teams can instantly address production issues flagged by operations staff, ensuring seamless coordination.
10. Scalability for Future Growth
As manufacturers expand operations or introduce new production lines, real-time monitoring solutions provide the scalability needed to support growth. These solutions adapt to changing demands without requiring a complete system overhaul.
Manufacturers looking to scale production can integrate real-time monitoring solutions with new equipment, gaining immediate visibility and control over operations as they grow.
Conclusion
Real-time monitoring is more than a technology upgrade, it's a strategic necessity for manufacturers looking to enhance efficiency, quality, and sustainability. Whether producing discrete components or managing continuous processes, having access to real-time insights empowers you to make better decisions and stay ahead of industry challenges.
At Gerrie Digital Industry Solutions, we're proud to support Canadian manufacturers with smart manufacturing solutions tailored to their unique challenges. As your local manufacturing partner, we're here to help you harness the power of real-time data to optimize your operations and achieve your goals. Let's connect and start your journey toward operational excellence. Schedule a complimentary consultation now.
Where Do I Go Next?
Schedule a complimentary technical consultation with our digital industry solutions experts for a tailored solution that fits your needs.
Contact Us Now To Learn More!
Head Office - Burlington, ON - Canada
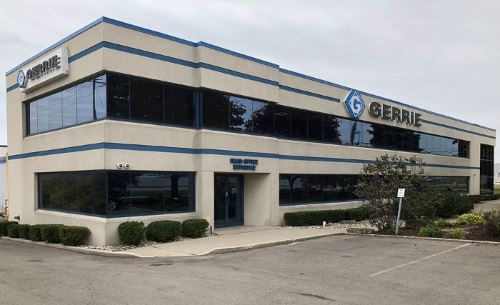
Email: [email protected]
Phone: (905) 681-3668
GERRIE DIGITAL INDUSTRY SOLUTIONS
Passionately Helping Customers Be More Successful by Delivering Exceptional Experiences.
Copyright © Gerrie Electric Wholesale Limited. All Rights Reserved
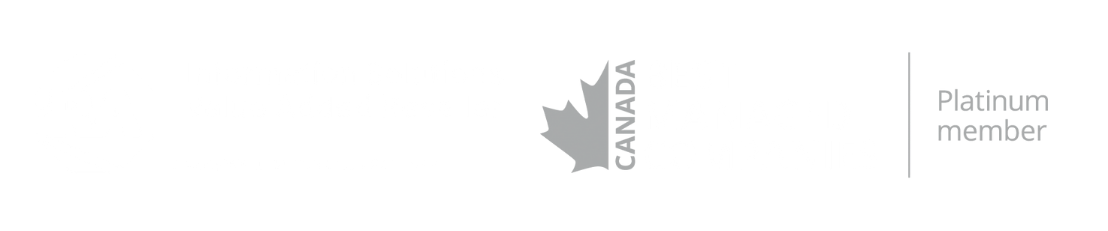